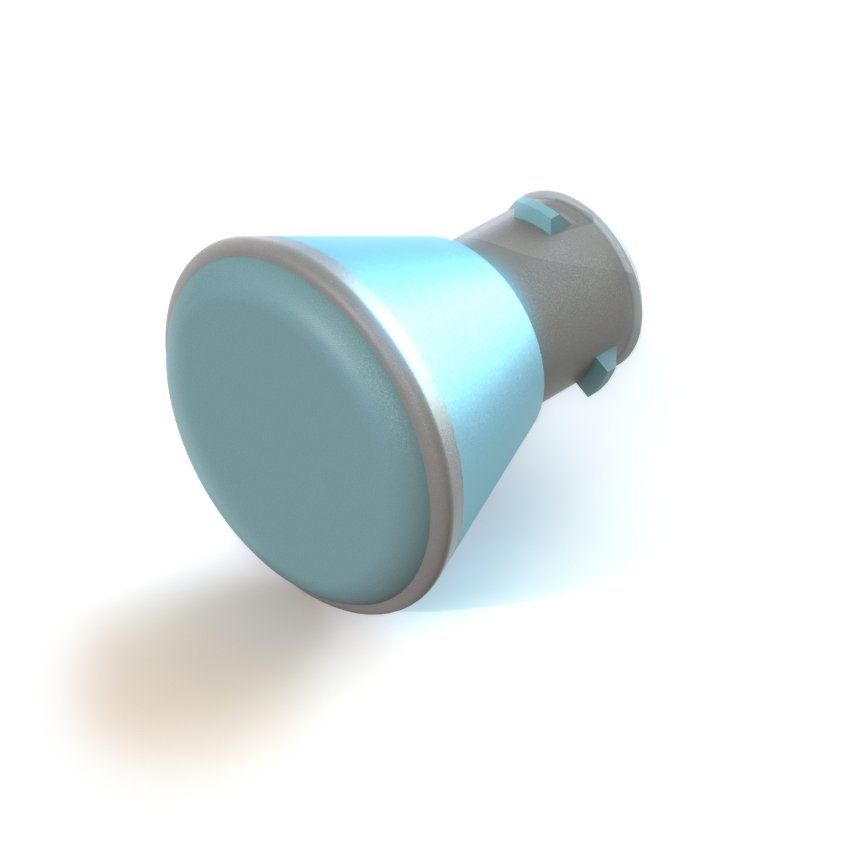
Medical
While at Huntleigh Healthcare
- Diagnostics Division, I designed an Obstetric Ultrasound Probe for the Dopplex range of handheld monitors. The probe was required to be IPX7 rated and meet the requirements of EN 60601 Medical Electrical Equipment and Systems. This was a successful product, and although I have left the company for several years, they have continued to incorporate this probe into their latest handheld devices.
Waterproof Probe (IPX7)
The brief was to design a new waterproof probe for an existing handheld obstetric unit. As the handheld unit was not being updated, the new design had to be compatible with its existing probe docking system. This determined the diameter and length of the probe, so any sealing system I designed had to meet these constraints.
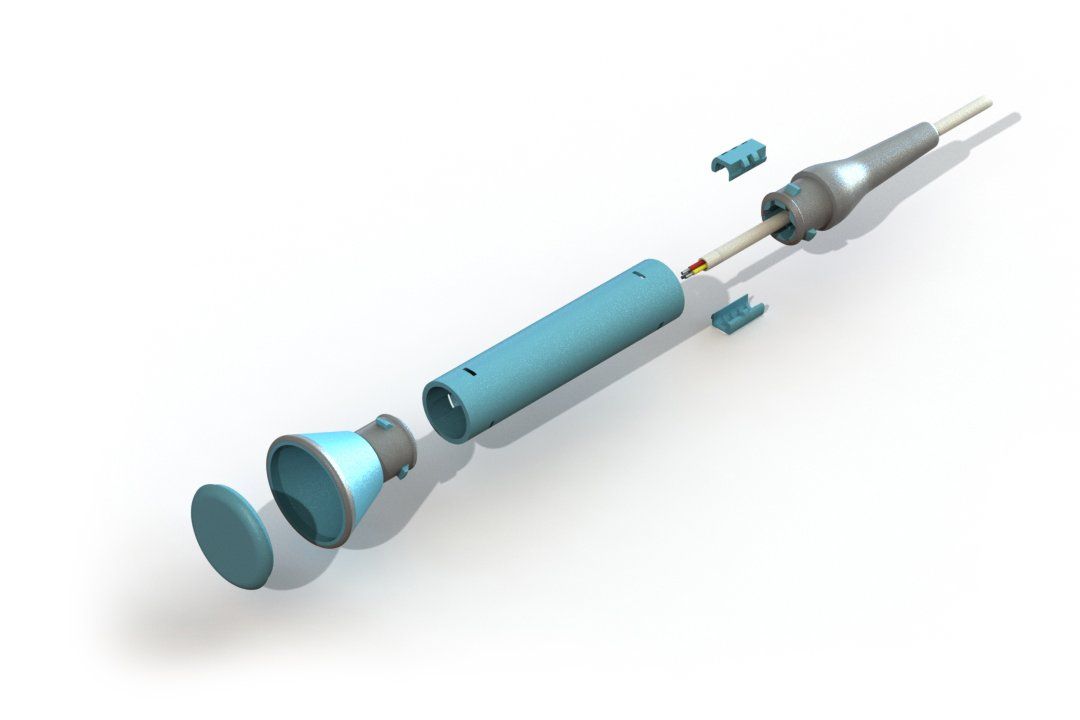
By using a mixture of medical-grade plastics and over-molded TPE materials, it was possible to injection mold the housing and the seal in one piece. This eliminated the need for secondary parts or sealing materials.
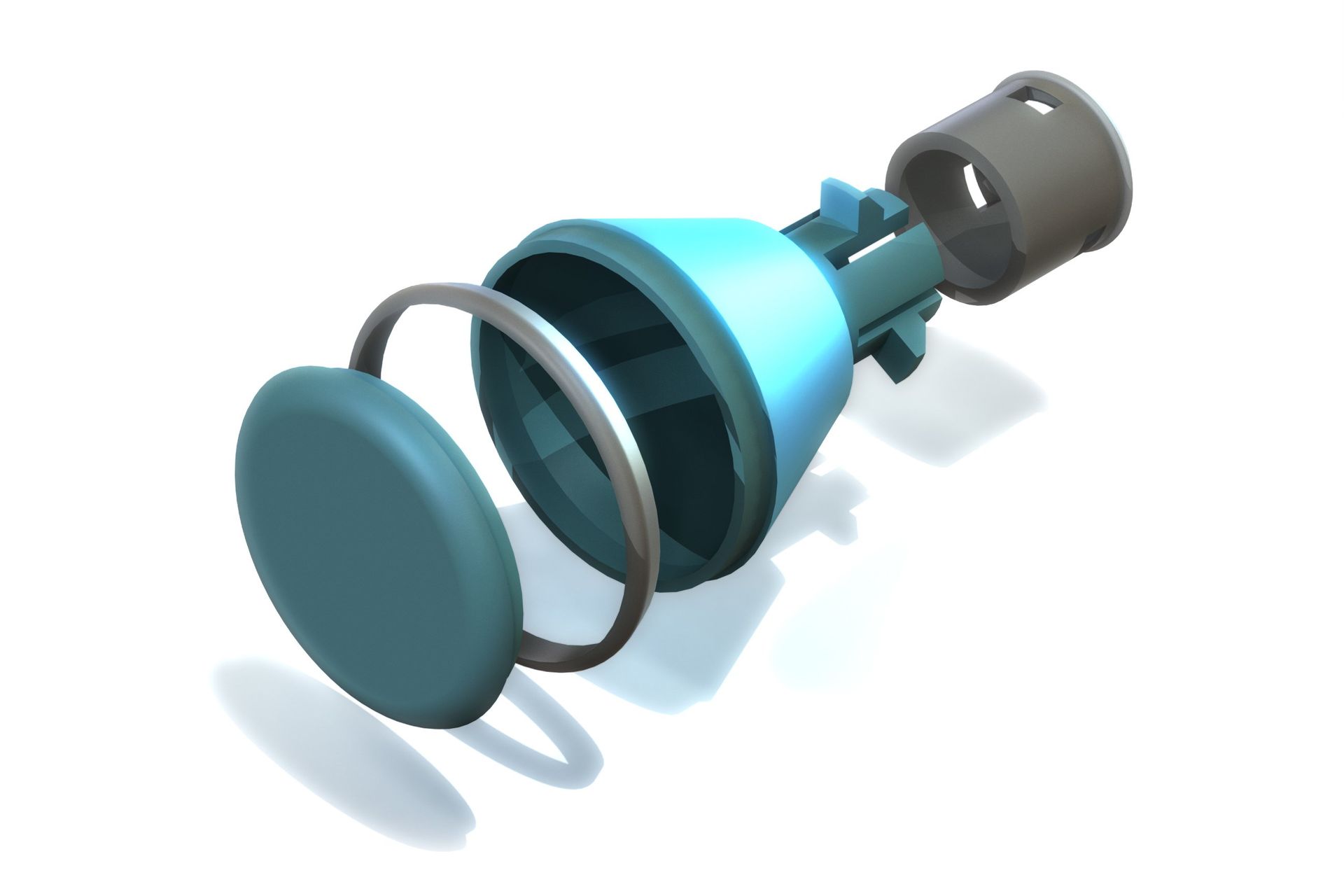
Both the probe head and tail had clipping features to speed up and simplify assembly. The tube body included guide features to aid in the alignment and force required to snap the product together. Notably, this probe was classified as a non-serviceable part for economic reasons. The option of using simpler parts and gluing or sealing all the components together was discussed. Although the individual part prices might have been slightly cheaper, the extra labor costs and the storage and handling of chemical bonding agents greatly outweighed the slight increase in part cost.
One factor often missed in calculating the expected build cost of a product is the space required for assembly. If there was a gluing element involved, the probes would have to be set aside to allow them to cure or dry. This would require space and disrupt the time and flow of the build process. This space could have been used to build other products, rather than holding multiple trays of drying probes.
One factor often missed in calculating the expected build cost of a product is the space required for assembly. If there was a gluing element involved, the probes would have to be set aside to allow them to cure or dry. This would require space and disrupt the time and flow of the build process. This space could have been used to build other products, rather than holding multiple trays of drying probes.
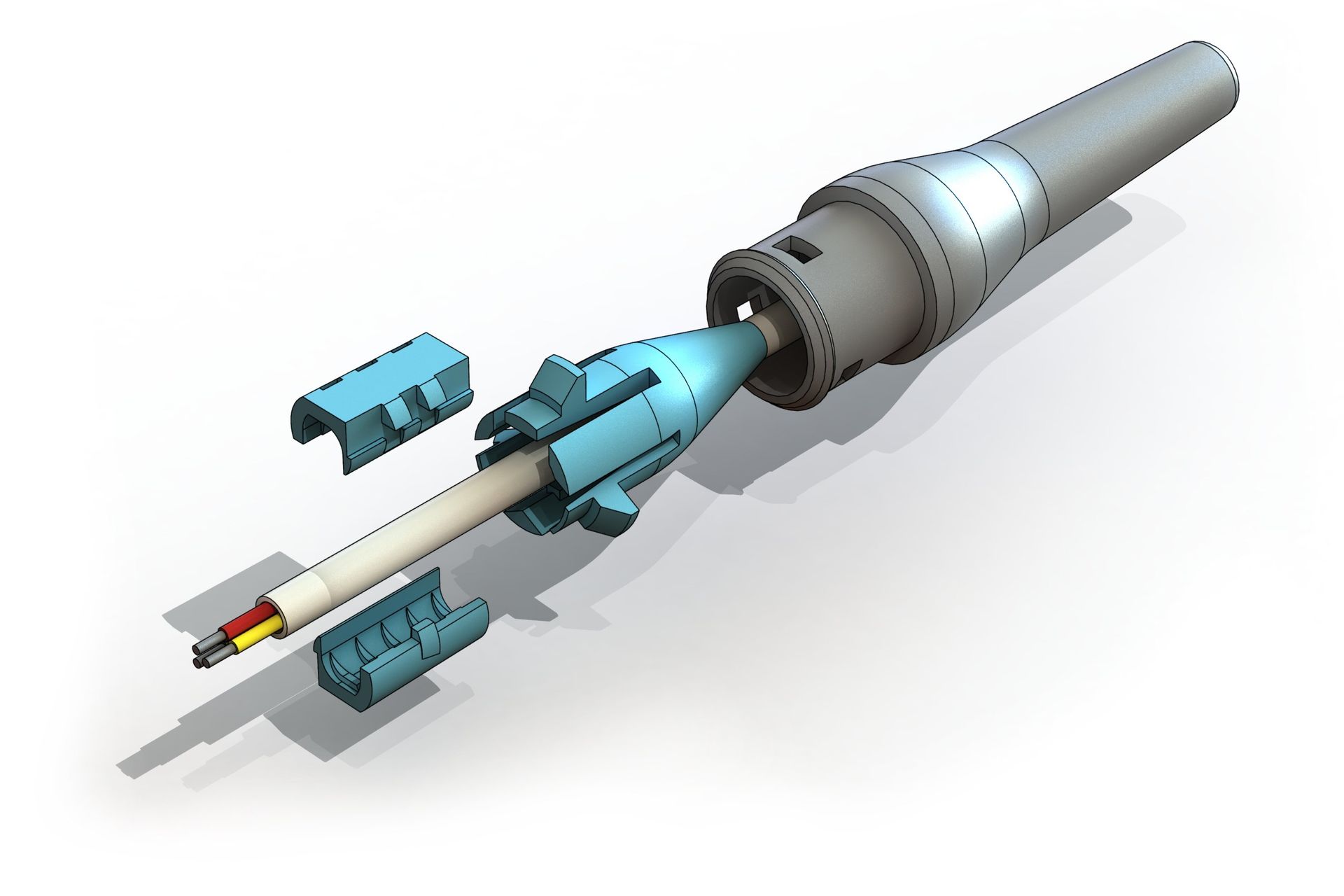
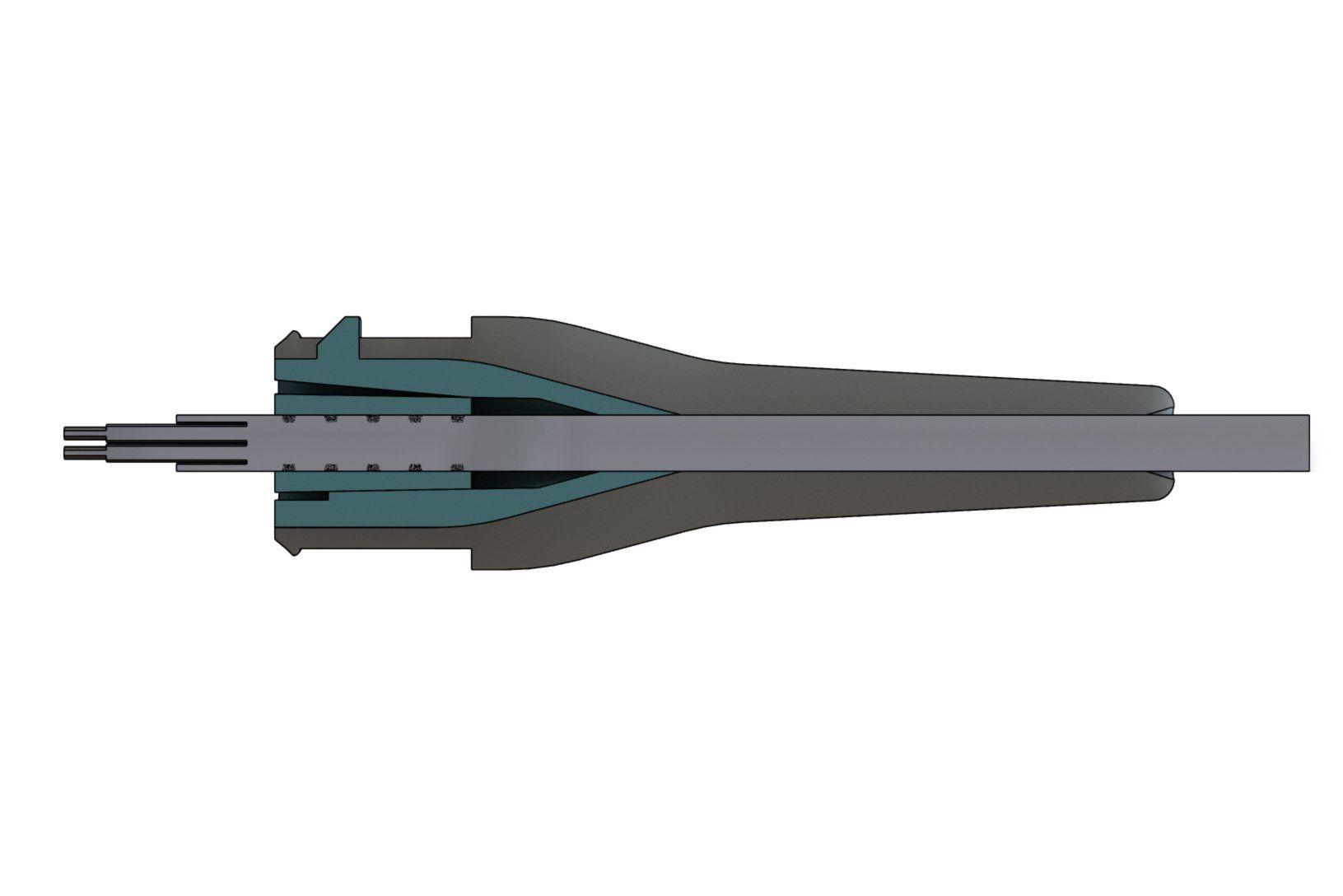
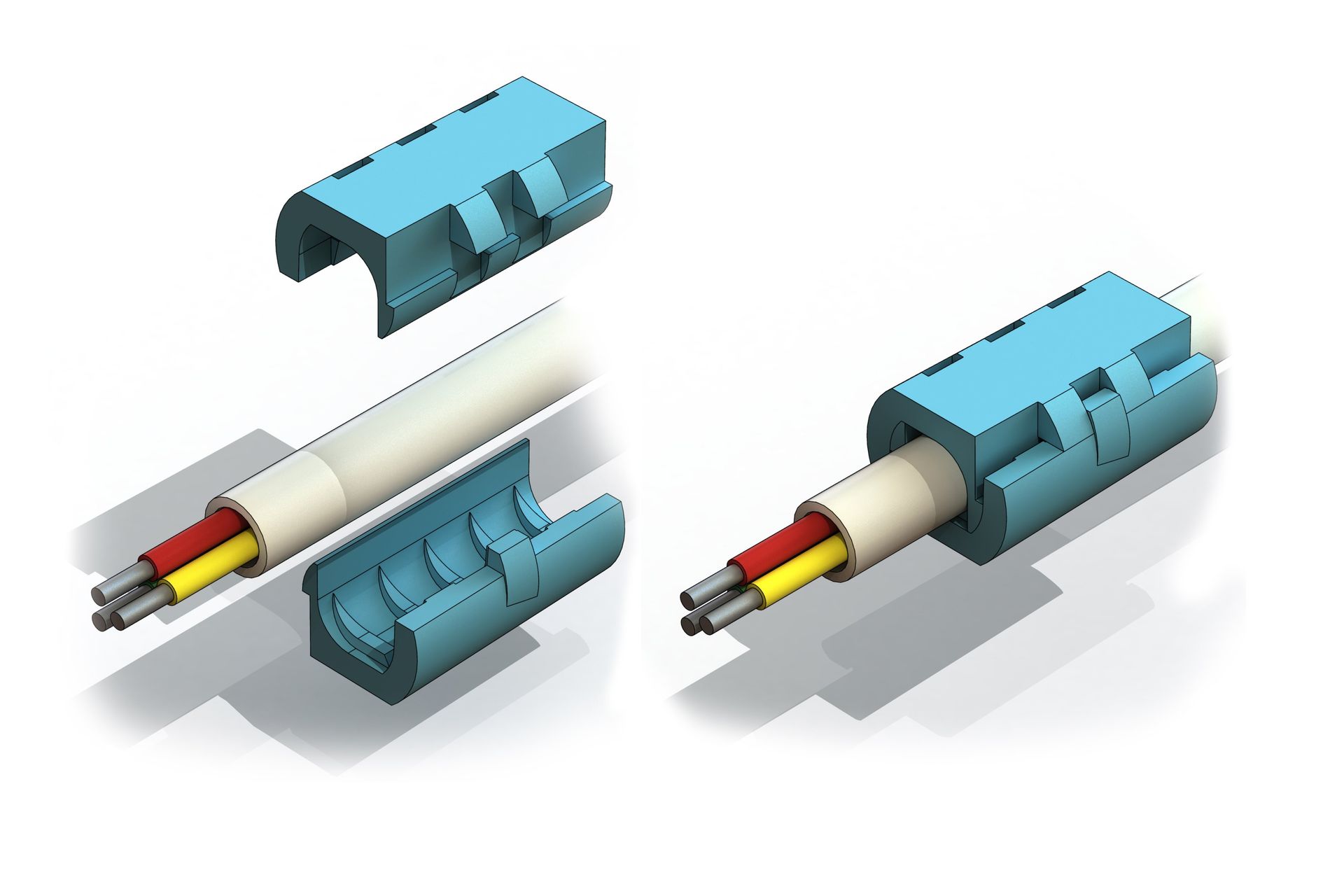
The tail section was comprised of multiple parts. To hold the cable in place, a component was designed to clamp the cable by clipping two pieces together. The inner surface of the clamp had small ridges that would bite into the cable sheath without causing damage.
The outer surface of the clamp was slightly tapered, as was the surface of the mating part in the grommet section of the tail. This design functions like a Morse taper, meaning that if the cable is pulled from the outside, the taper increases the force applied to the cable sheath. This prevents any strain from being applied to the solder joints between the cable and the PCB.
The outer surface of the clamp was slightly tapered, as was the surface of the mating part in the grommet section of the tail. This design functions like a Morse taper, meaning that if the cable is pulled from the outside, the taper increases the force applied to the cable sheath. This prevents any strain from being applied to the solder joints between the cable and the PCB.
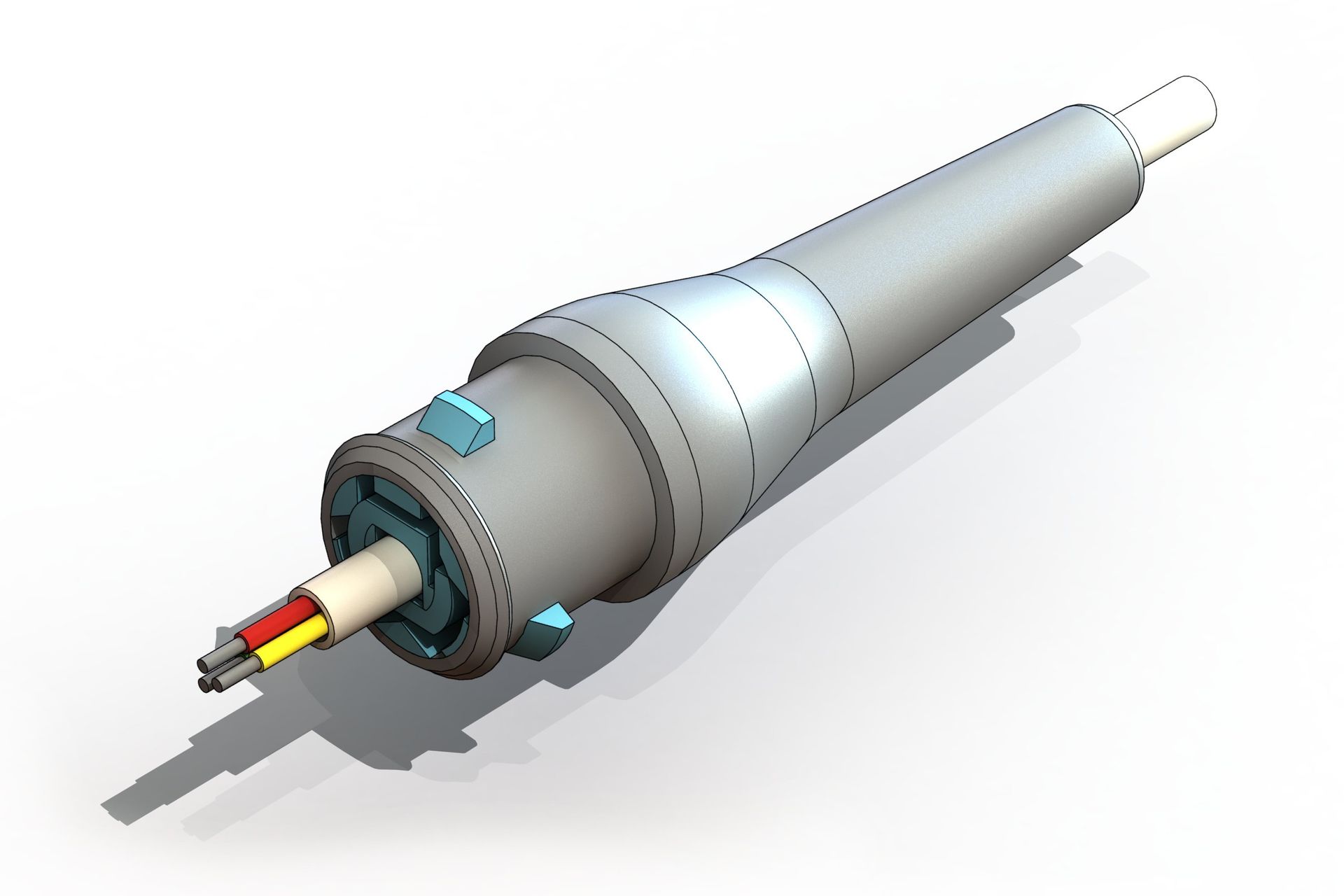
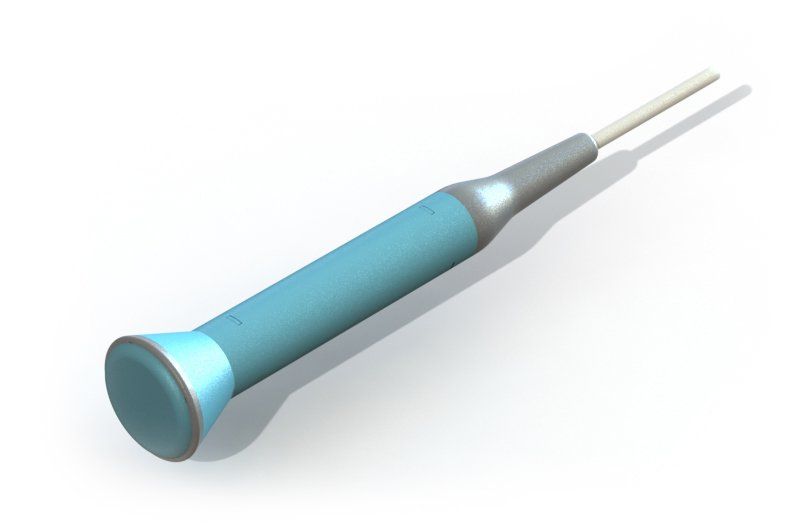
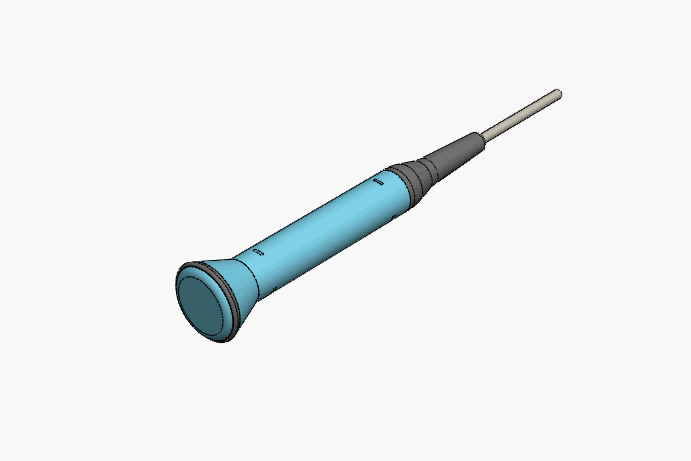