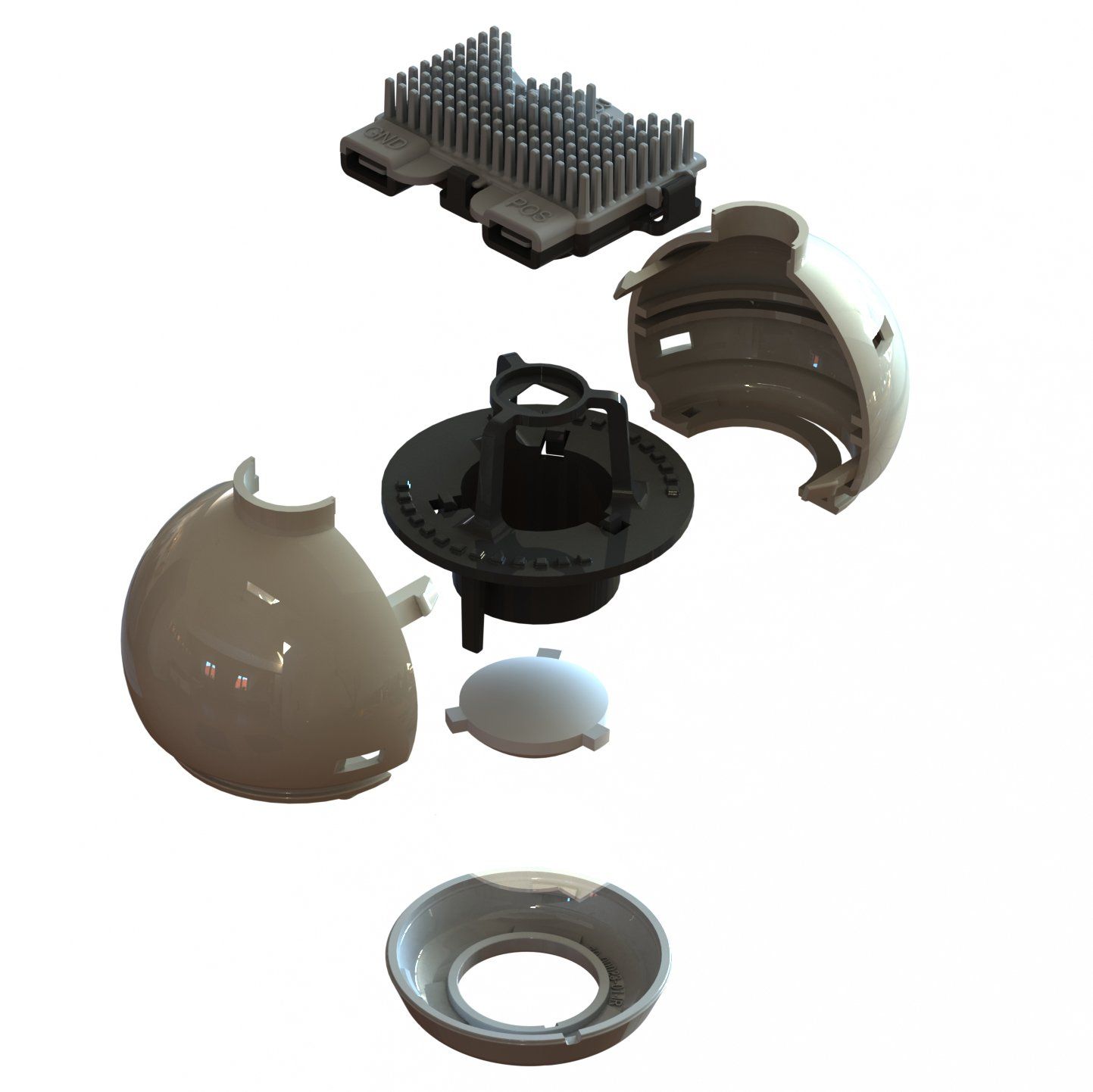
Aerospace
STG Aerospace
is an international industry leader in the development, design, and manufacture of aircraft cabin lighting solutions for both commercial and military sectors.
The example below demonstrates how applying modern technology and design to a dated aircraft interior can significantly enhance the customer's comfort experience.
The example below demonstrates how applying modern technology and design to a dated aircraft interior can significantly enhance the customer's comfort experience.
Boeing Reading Light
The current reading light in Boeing
aircraft uses a simple incandescent bulb, which results in a non-controlled light pattern that often spills onto adjacent passengers. The color rendering can also make the cabin look old and tired. The project required replacing this system with an LED and using state-of-the-art components. Any solution needed to fit into the existing Passenger Service Unit (PSU) without increasing the product's weight.
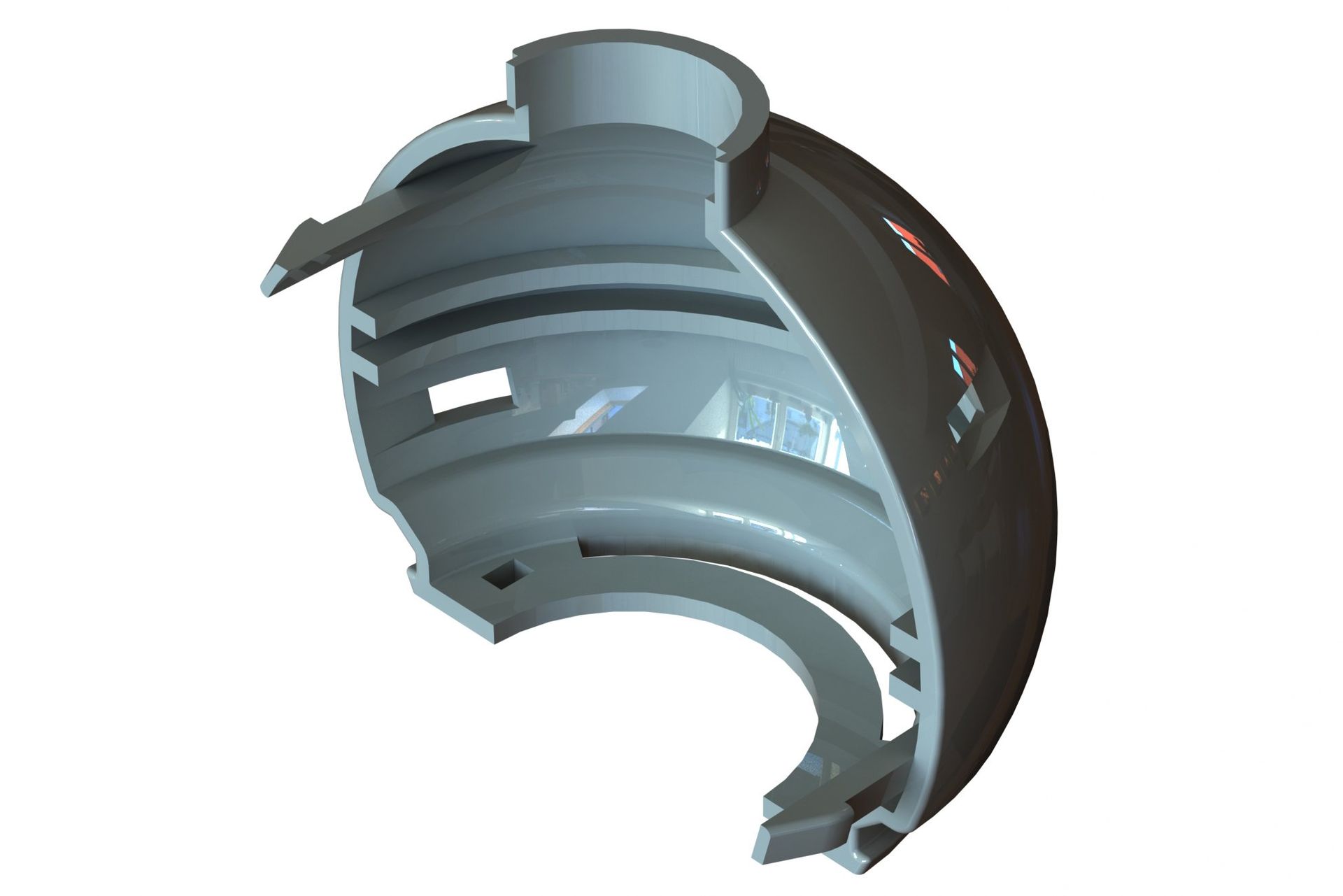
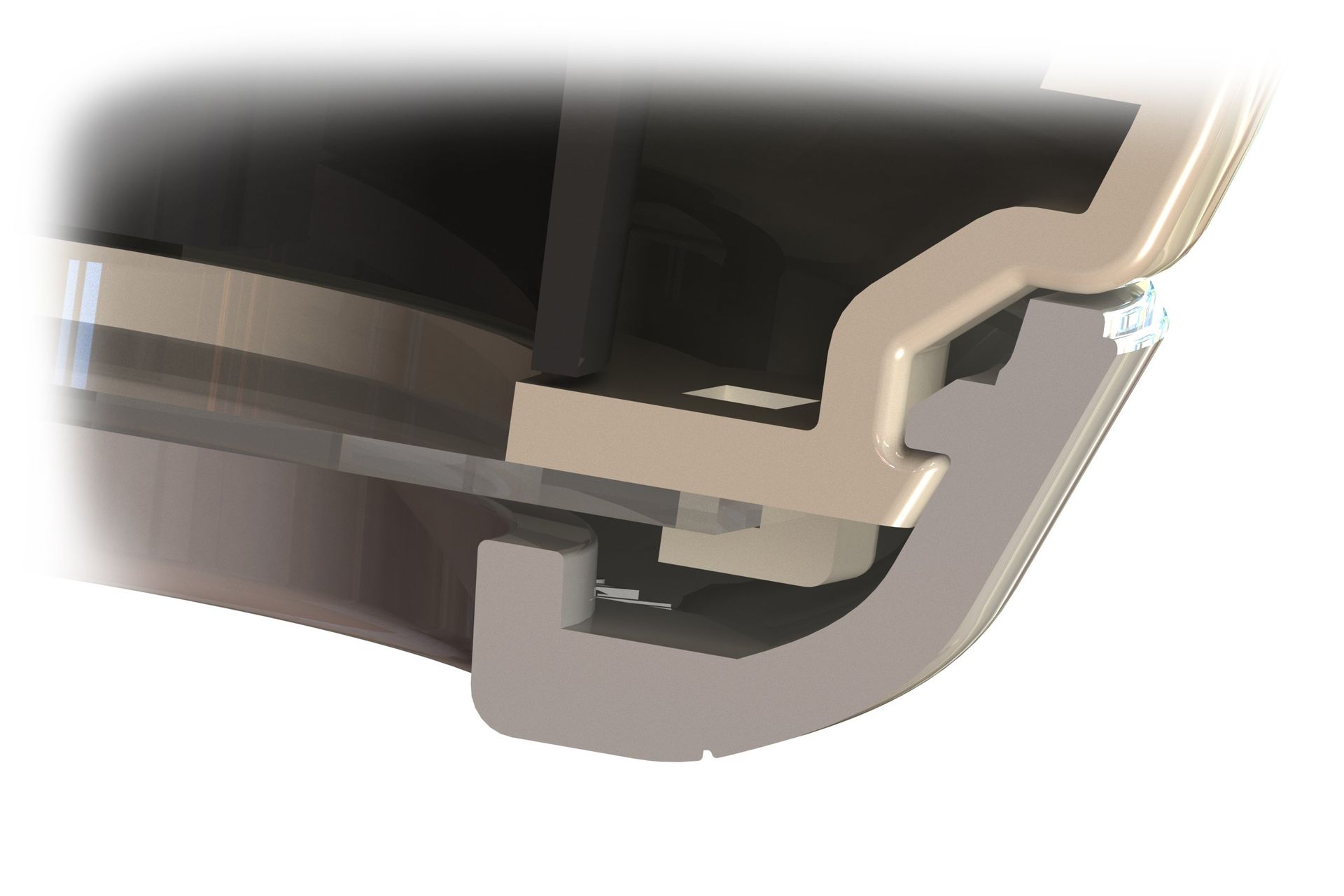
From the start, the goal was to minimize the part count and ensure that the system was designed for efficient assembly and installation. As labor time is often more expensive than part cost, all needs for secondary operations such as gluing and fasteners were designed out. The design utilized containment and clipping features to hold and position parts. As a result, the entire assembly could be put together manually in under one minute.
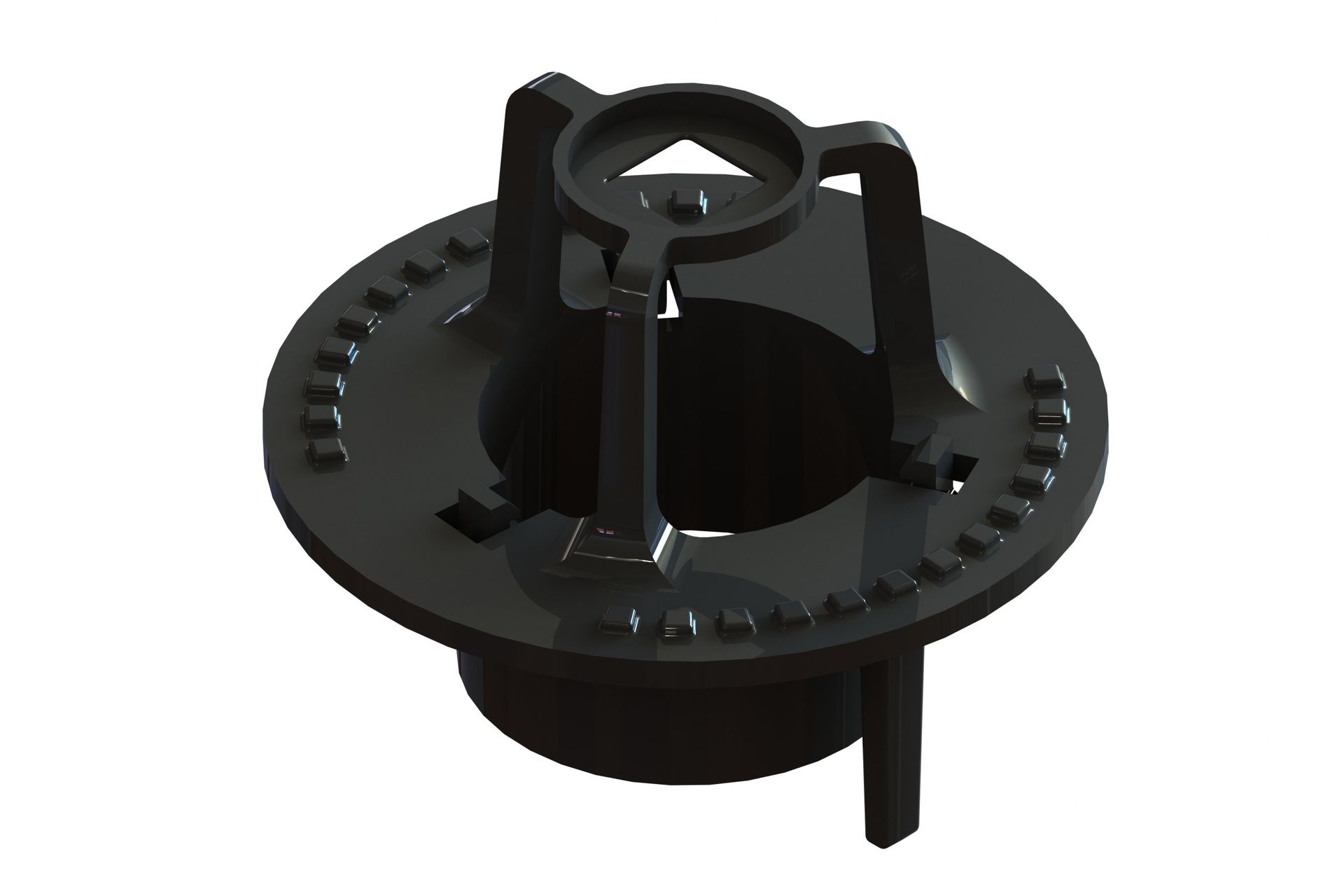
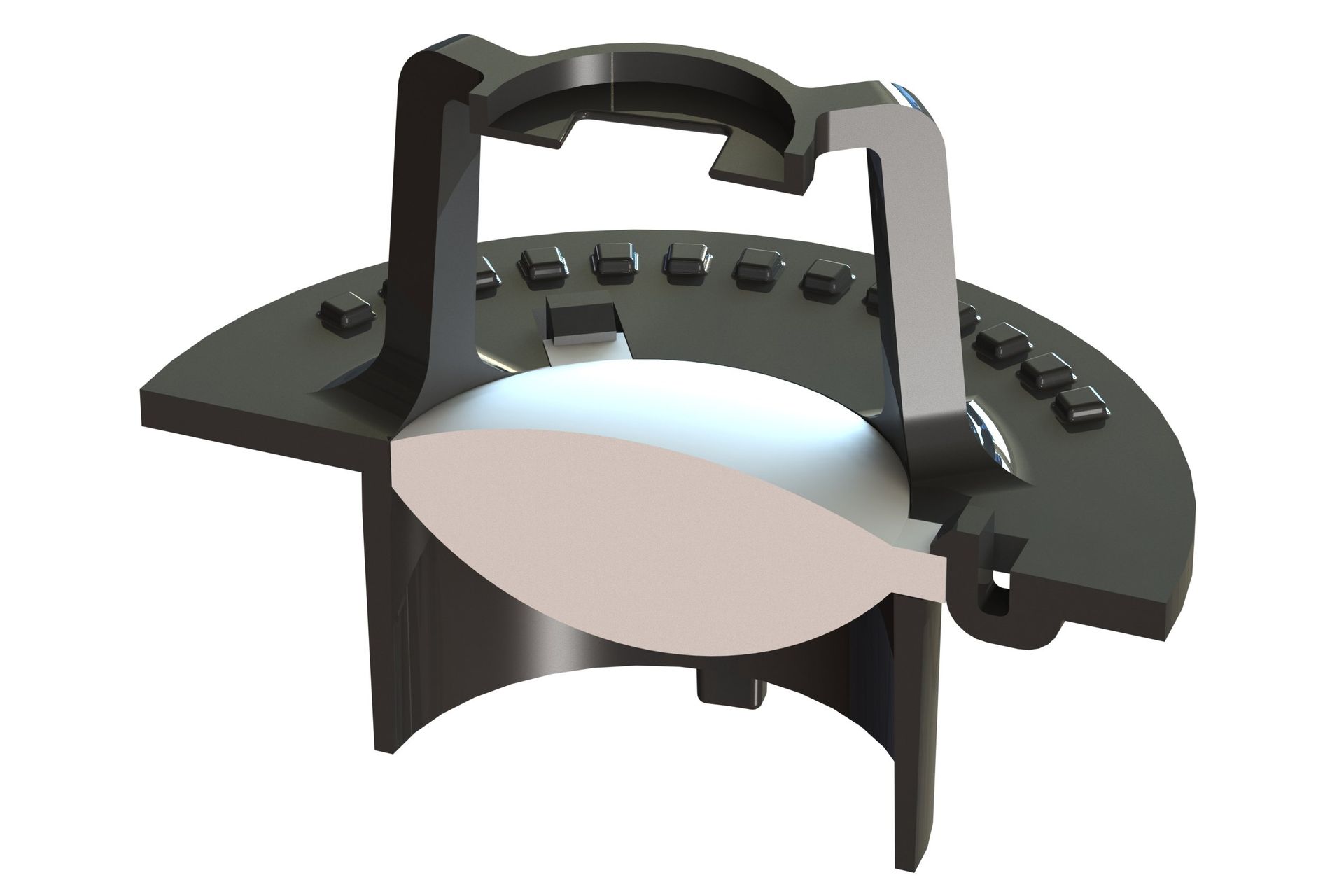
Before committing to tooling, all parts were rapid prototyped to prove the concept. For this project, both machined parts and SLS techniques were used. This approach allowed for small adjustments to be made to the design early in the timeline, preventing costly and time-consuming corrections later on. It also enabled buy-in from other stakeholders within and outside the company before committing to tooling. This fostered confidence in our direction and facilitated a smoother transition through stage gates, ensuring project deadlines were met. Additionally, it gave me more time to explore new concepts I had not previously worked with in my career. For example heat management in an enclosed space. Due to weight restrictions and space limitations, it was not possible to have a separate heat sink for the product.
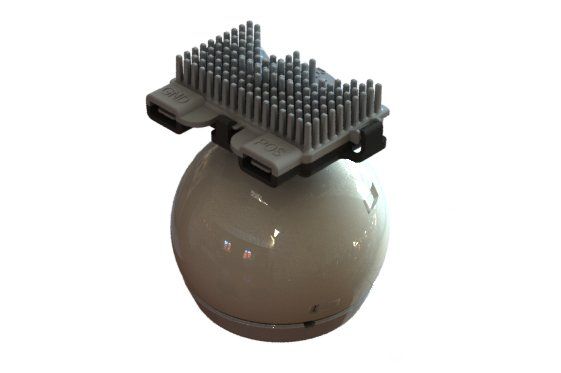
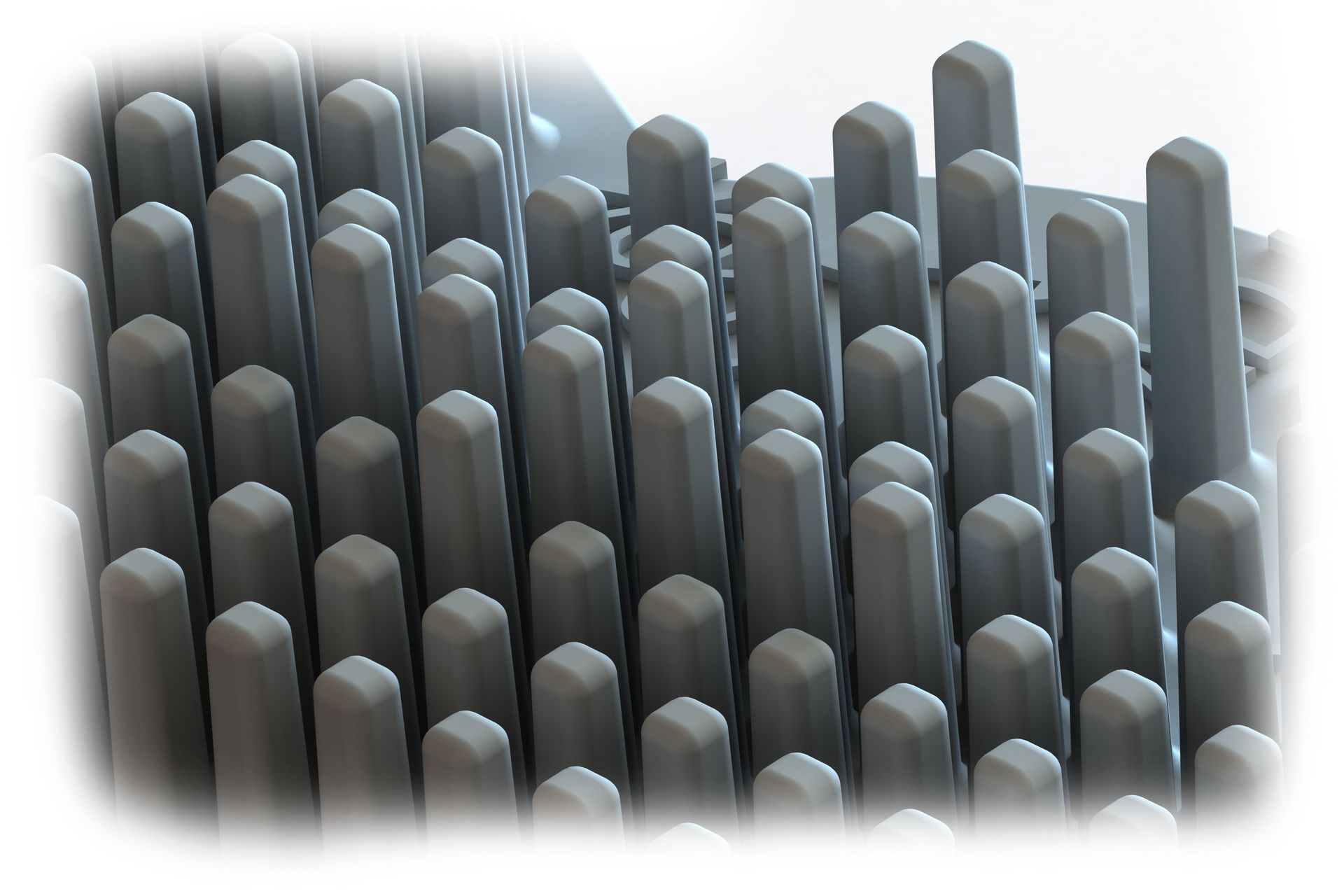
I designed the top housing cover to double as the heat sink. Most plastics are heat insulators, but through research and consultation with material specialists, a thermally conductive Nylon was chosen. Calculations were made to estimate the surface area required to dissipate the heat energy within the system. The vanes were carefully positioned and shaped to achieve this. Conductive versions of Nylon are more brittle than standard versions, which had to be considered when designing the assembly. Consequently, clipping features were moved to the lower molding.
For more information about this product, visit: www.stgaerospace.com
For more information about this product, visit: www.stgaerospace.com
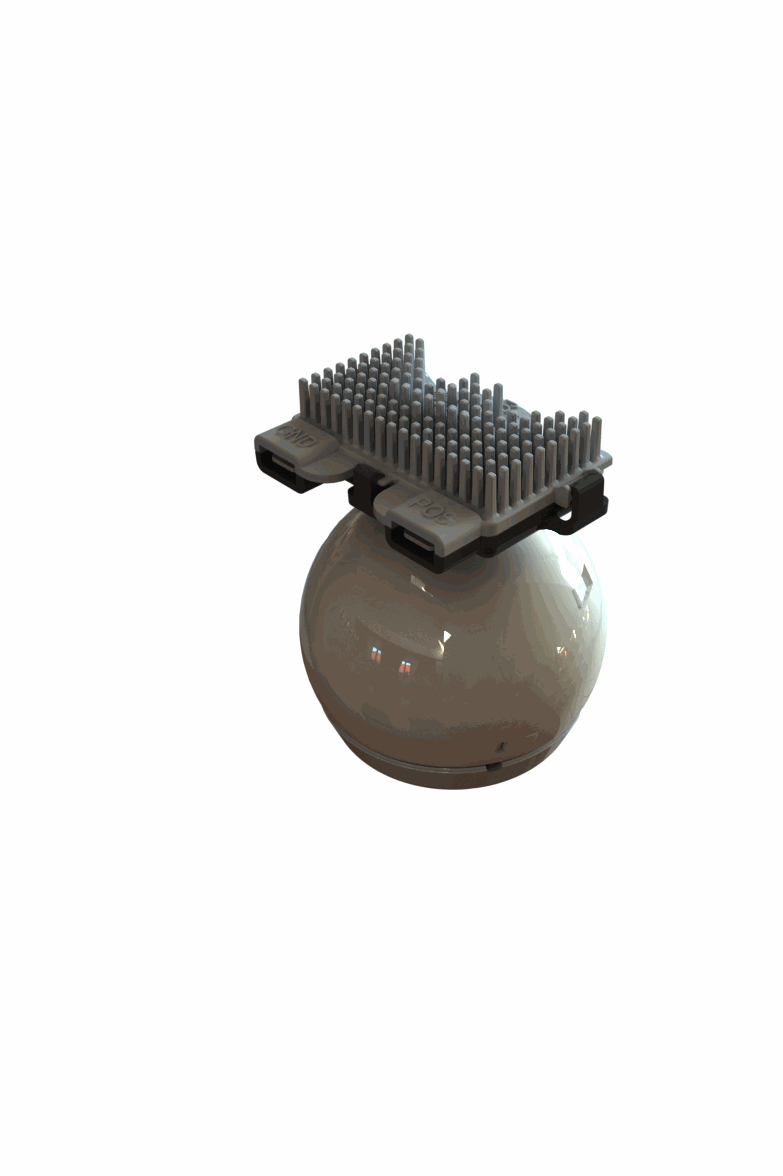