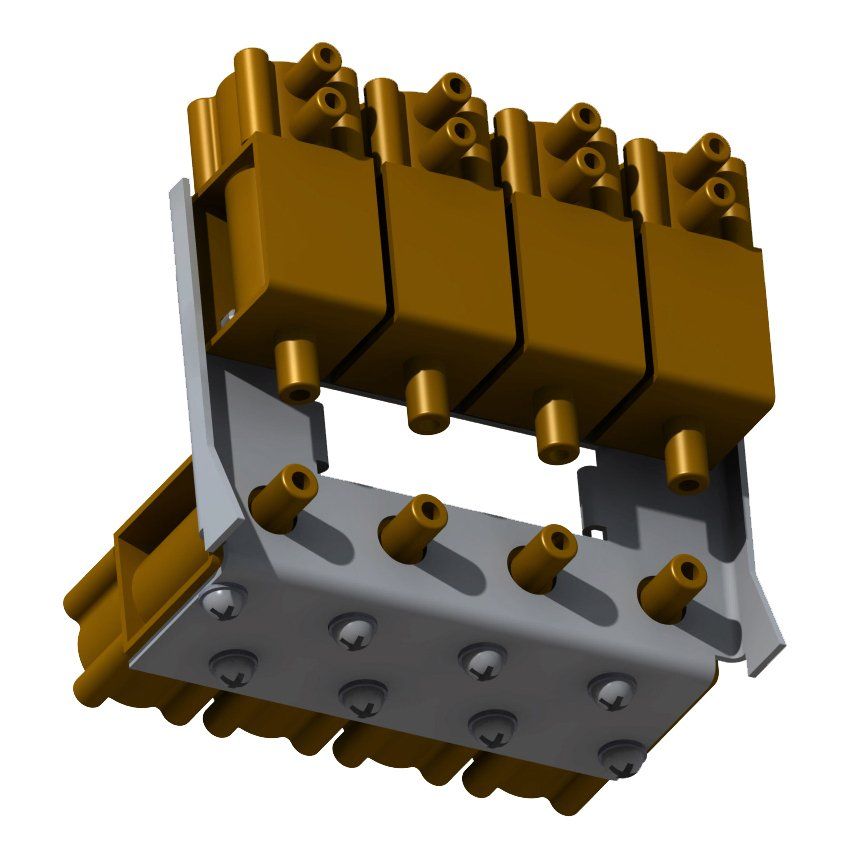
Medical
While at Huntleigh Healthcare
- Diagnostics Division, I worked on a number of market-leading products.
In many cases, customers requested specific OEM modules to be fitted to the devices. To accommodate these requests and remain price competitive, interface metal plates were designed into the product. This allowed for quick customer configuration and the rapid introduction of any new OEM modules that entered the market, without the need for expensive and time-consuming injection molding tooling modifications.
In many cases, customers requested specific OEM modules to be fitted to the devices. To accommodate these requests and remain price competitive, interface metal plates were designed into the product. This allowed for quick customer configuration and the rapid introduction of any new OEM modules that entered the market, without the need for expensive and time-consuming injection molding tooling modifications.
Pneumatic Assembly
A 1.2mm thick sheet metal bracket was designed to hold eight solenoid valves, each weighing 0.08kg (1.8lbs). In addition to the configuration flexibility mentioned earlier, this design allowed for a sub-assembly to be built separately from the main product. This improved the design for assembly by keeping the mechanical process away from the expensive electronics that could have been damaged during fitting. The design also had to meet the requirement of passing a 1.2m (4') drop test without deforming or breaking.
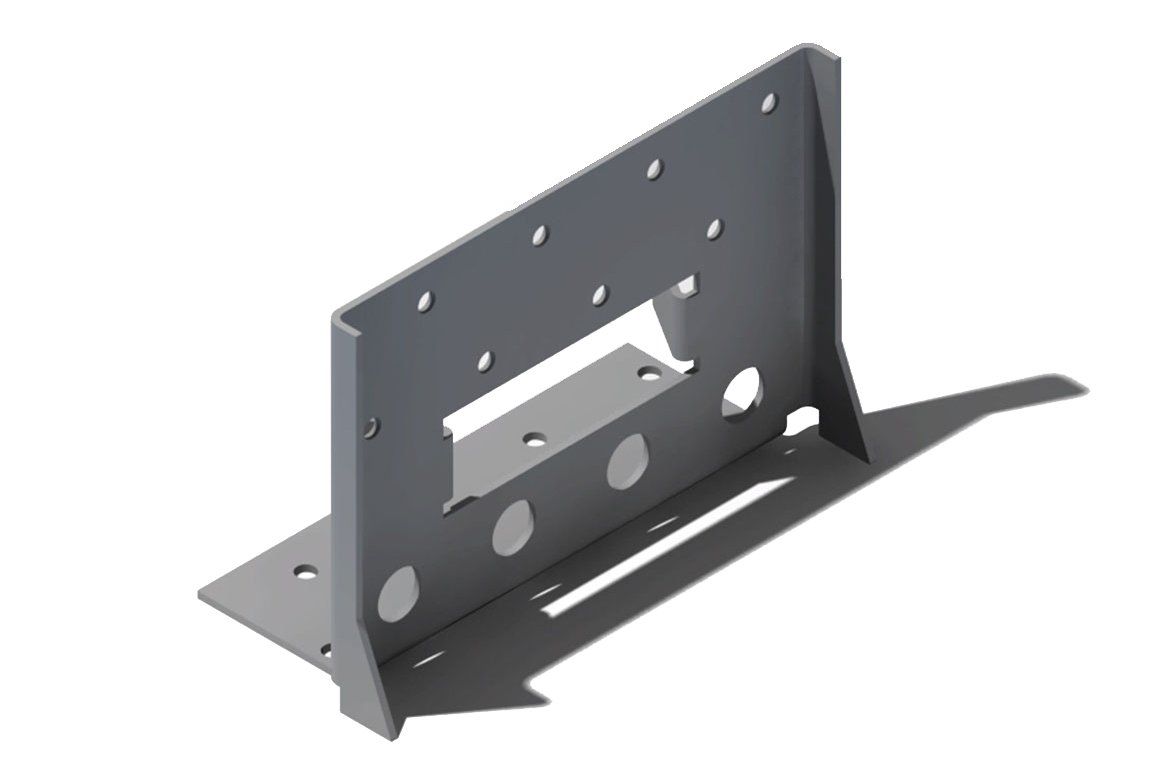
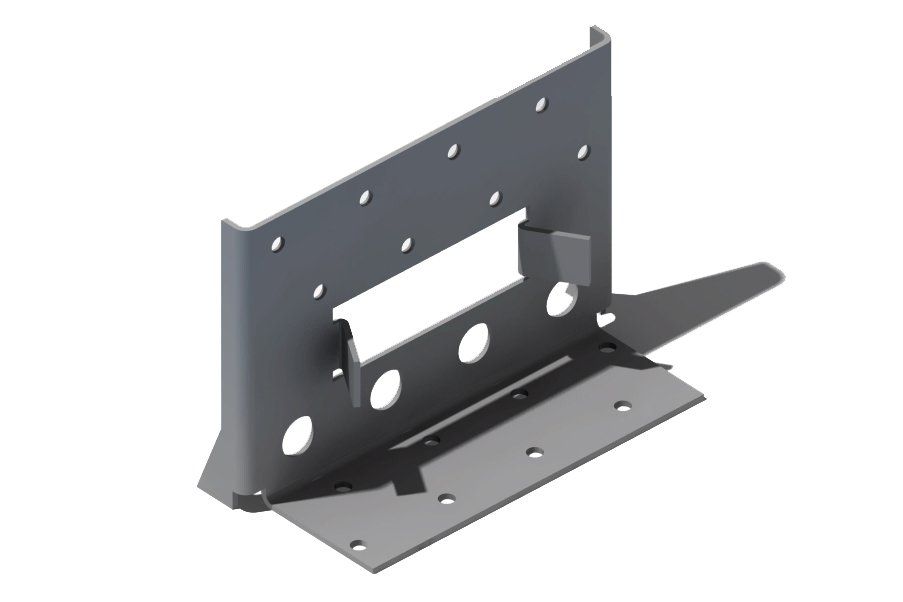
To achieve this, I used multiple bend relieves and changes in direction to stiffen the material's profile. Where possible, I shaped cutouts and edges to prevent tearing or creasing. In the bottom right image, the opening was added to improve the design for assembly, allowing the pneumatic tubes to pass through, making their path shorter, easier to manage, and overall reducing material and labor costs. However, rather than wasting the material in this area, I used it as a brace to stiffen the assembly.
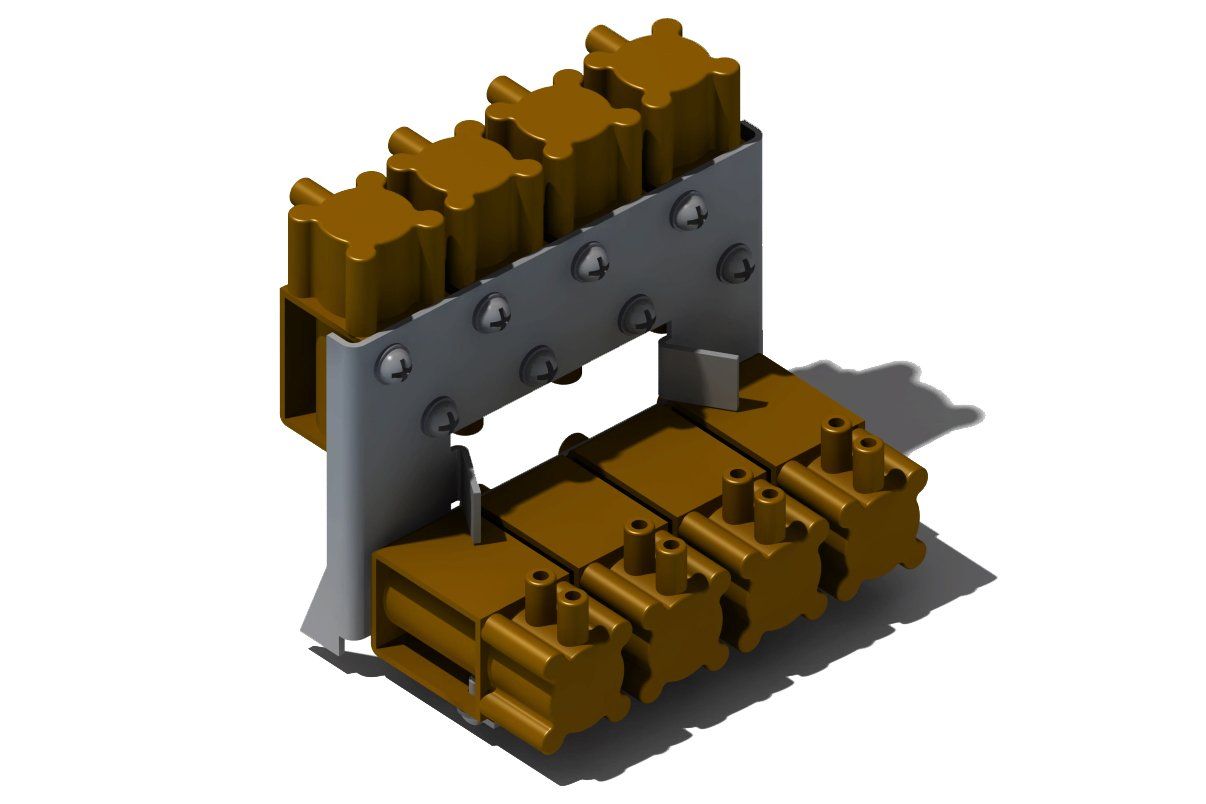
